Полимерное оборудование: виды и функции
Ниже перечислены все основные виды оборудования, так или иначе предназначенные для изготовления изделий из полимеров. Ниже вы найдете активные ссылки на то оборудование, которое поставляется компанией Интерпласт.
Оборудование для формования изделий |
||||||||||||||||||
Оборудование для прессования |
Оборудования для изготовления стеклопластиков и углепластиков |
Оборудование для производства ворсовых материалов |
Оборудование для изготовления изделий методами вакуумного, пневматического и механического формования |
Оборудование для изготовления изделий методом литья под давлением |
||||||||||||||
Оборудование для грануляции |
Оборудование для изготовления изделий методом непрерывного выдавливания (экструдеры) |
Оборудование для каландрования |
Оборудование для изготовления изделий из древопластиков |
Оборудование для пропитки, промазки и печати |
Нетканых и флокированных материалов |
Инструмент и оборудование для обработки и сварки пластмасс |
||||||
Пресс-формы |
Оборудование для сварки |
Оборудование для нанесения покрытий |
Оборудование для формования изделий
Оборудование для изготовления изделий методом литья под давлением
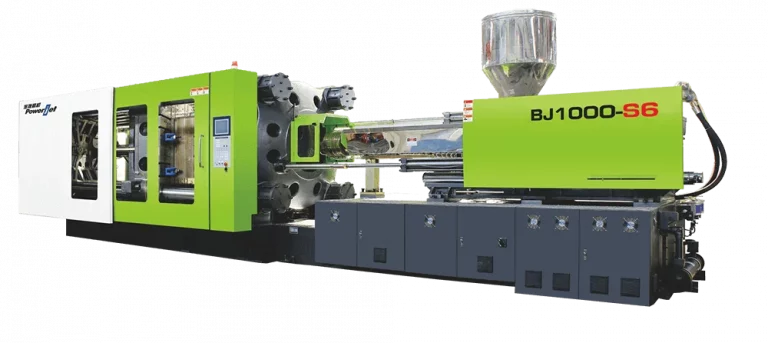
Оборудование для литья под давлением
Литье под давлением является одним из самых распространенных методов переработки пластмасс.
Сущность процесса заключается в том, что материал разогревается до пластического состояния в специальном цилиндре и инжектируется из него под высоким давлением и с большой скоростью в литьевую форму.
Литьевые машины классифицируют по мощности, конструкции и типу привода. Производственную мощность литьевых машин определяют в кубических сантиметрах впрыскиваемого материала, расходуемого на изготовление одной отливки, она колеблется от нескольких до десятков тысяч кубических сантиметров.
По конструкции литьевые машины подразделяются
- в зависимости от нагнетающего устройства — на поршневые и червячные;
- от направления разъема форм — на горизонтальные, вертикальные и угловые;
- от количества форм — на одноформовые и многоформовые (ротационные);
- от количества инжекционных цилиндров — на одно- и многоцилиндровые;
- от наличия механизма предварительной пластикации — без предварительной пластикации (с совмещенной пластикацией) и с предварительной пластикацией;
- от типа привода — на механические, гидравлические, гидромеханические, пневматические, пневмогидравлические.
Наибольшее распространение получили горизонтальные одночервячные с совмещенной пластикацией ТПА. Они обеспечивают объемы впрыска от 4 см³ до 70 000 см³ при усилии запирания формы от 25 до 60 000 кН.
Оборудование для изготовления изделий методом непрерывного выдавливания (экструдеры)
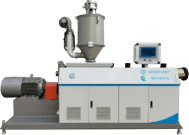
Экструдеры для пластика
Под непрерывным выдавливанием (экструзией) понимают процесс придания предварительно пластицированному материалу определенной формы при продавливании через оформляющую головку.
Агрегаты, на которых осуществляется процесс экструзии называются экструдерами или червячными прессами.
Червячные прессы различают:
- в зависимости от количества червяков (шнеков) — одночервячные (одношнековые) и многочервячные (многошнековые);
- в зависимости от геометрической формы червяка — обычные и специальных типов;
К прессам обычного типа относят машины с цилиндрическим червяком, с убывающим объемом винтового канала; к прессам специального типа –машины с коническим и параболическим червяком, с полым червяком и внутренней нарезкой, с телескопическим червяком и несколькими загрузочными отверстиями, с наборным червяком из дисковых кулачков, а также прессы с червяками специальной формы для создания, смешивающего и гомогенизирующего эффекта;
- в зависимости от направления вращения червяков прессы с двумя червяками — с одинаковым направления вращения (со-направленным) и с взаимнопротивоположным направлением вращения (встречное вращение);
- в зависимости от отношения длины червяка (L) к его диаметру (D) — с коротким червяком (L<10D) и длинным червяком (L>10D);
- в зависимости от частоты вращения червяка — тихоходныные (п<150 об/мин) и быстроходные (n>150 /мин);
- в зависимости от способа обогрева цилиндра — с электрическим, паровым обогревом или обогревом жидкими теплоносителями;
- в зависимости от способа охлаждения цилиндра — с водяным или воздушным охлаждением;
- в зависимости от конструкции станины — рамной(сварной), литой конструкции и червячные прессы с вынесенным цилиндром;
- в зависимости от привода — с механическим регулированием частоты вращения червяка и электрическим регулированием с регулируемым приводом на основе двигателя постоянного или переменного тока.
Кроме червячных прессов существуют дисковые, валковые и планетарные экструдеры.
Экструдеры служат базовыми агрегатами в экструзионных линиях различного назначения: трубные, линии для формования различных профилей, линии для изготовления выдувных пленок, линия для производства плоских пленок и листов.
Оборудование для грануляции
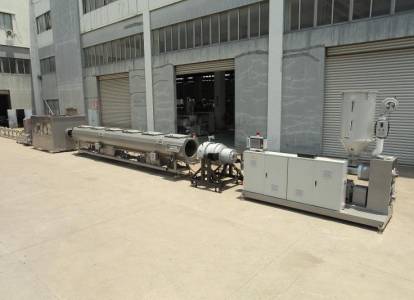
Полимерное оборудование: виды и функции
Процесс гранулирования применятся к термопластичным материалам.
Преимущества гранулированных материалов перед порошкообразными заключатся в удобстве их транспортирования, отсутствия запыленности рабочих мест, уменьшения потерь материалов, высокой производительности, а также в более простой конструкции загрузочных узлов.
В зависимости от способа изготовления гранулы могут быть кубической, цилиндрической, эллипсоидной и шарообразной формы.
В зависимости от способа охлаждения грануляторы подразделяют на грануляторы с воздушным и водяным охлаждением.
В зависимости от способа резки грануляторы подразделяют на грануляторы с резкой на фильере (горячая резка) и стренговые грануляторы (холодная резка) с резкой на отдельном узле при помощи ножей.
Грануляторы с водяным охлаждением и резкой на фильере называют водокольцевыми, а стренговые грануляторы с водяным охлаждением-погружными.
Способ и схема гранулирования выбираются в зависимости от свойств гранулируемого материала.
Оборудование для формования изделий методом прессования
Таблеточные машины
Таблетирование – процесс (предшествующий прессованию) изготовления из порошка волокнистого термореактивного материала таблеток определенной формы, размеров и плотности. Таблетирование применяется для повышения теплопроводности материала, удаления из него воздуха, уменьшения размеров загрузочной камеры пресс-формы.
Таблеточные машины в зависимости от типа провода подразделяют на механические, гидравлические и пневматические. В зависимости от расположения пуансона и матрицы на горизонтальные и вертикальные.
Аппараты для предварительного подогрева материала
Термореактивные материалы перед изготовлением из них изделий методом прессования нагревают, что позволяет снизить давление прессования и сократить время, необходимое для отверждения.
Предварительно реактопласты можно подогревать в шкафах-термостатах, в контактных нагревателях и генераторах ТВЧ.
Гидравлические прессы
Прессование – процесс получения из пластмасс изделий заданных размеров и конфигурации в пресс-форме под давлением пуансона.
Изделия прессуют двумя способами: компрессионным (прямым) и трансферным (литьевым).
Различают также холодное компрессионное прессование и горячее компрессионное прессование.
Литьевое прессование основано на применении загрузочной (передаточной) камеры, из которой подогретый материал после достижения нужной пластичности нагнетается в соответствующую форму.
Гидравлические прессы подразделяют:
- по силе прессования — на прессы низкого давления(от 0,25 до 10 МН/м2) и высокого давления (от 10 до 50 МН/м2);
- по конструкции станины — на колонные и рамные;
- по направлению закрывания пресс-формы — вертикальные, горизонтальные и угловые;
- по типу привода — с индивидуальным приводом и групповым приводом;
- по направлению рабочей силы — с верхним, нижним и комбинированным давлением;
- по количеству главных рабочих цилиндров — одноцилиндровые и много цилиндровые;
- по конструкции главного гидроцилиндра — с цилиндром одностороннего действия и возвратными цилиндрами двухстороннего действия, снабженных диффенциальным плунжером;
- по количеству прессующих плит — одно-, двух- и многоэтажные;
- по периодичности работы пресса — цикличные и карусельные;
- по способу управления — с ручным, полуавтоматическим и автоматическим управлением.
Роторные прессы значительно сокращают время прессования. Роторные прессы делятся на револьверные (с периодическим поворотом ротора на определенный угол) и ротационные (с непрерывным вращением ротора).
Автоматические роторные линии позволяют полностью автоматизировать процесс прессования.
Прессы для трансферного прессования применяются для прессования термореактивных материалов со сложной конфигурацией, требующих высокой точности.
Оборудование для изготовления изделий методами вакуумного, пневматического и механического формования
В качестве исходного сырья в процессах вакуумно-пнематического и механического формования используются полимерные листы и пленки.
Сущность этих процессов заключается в том, что предварительно нагретый листовой материал приобретает заданную форму под действием атмосферного давления (вакуумное формование), избыточного давления воздуха (пневматическое формование) или механических сил (механическое формование). В ряде случаев используется смешанный тип воздействия на листовой материал.
Соответственно различают вакуум- и пневмоформовочные машины, а также машины для механического формования, которые называют также термоформовочными машинами.
Оборудование для каландрования
Каландровый метод получения пленки основан на непрерывном формовании из расплава полимерного материала пленочного полотна в зазоре между вращающимися навстречу друг другу валками. При этом варианты взаимного расположения валков каландров могут быть различными.
Следует различать собственно каландровый процесс, отличительной особенностью которого является образование «вращающихся» запасов между формующими валками и квази каландровый процесс, осуществляемый на гладильных каландрах, в результате которого происходит только поверхностный контакт пленки и формующих валков.
Наибольшее распространение каландровый способ производства получил для производства пленок ПВХ.
Каландровые линии для производства ПВХ-пленок подразделяются на прецизионные и непрецизионные. Первые предназначены для изготовления высокоточных пленок, вторые – для пленок общего назначения.
Каландры классифицирую в зависимости от взаимного расположения валков: а – I-образное; б – F(Г)-образное; в – L-образное; д – Z-образное.
В современную универсальную каландровую линию для изготовления высокоточных ПВХ-пленок должны входить следующие узлы и элементы:
1) Узел подготовки сырья, включающий диспергирующее, смесительное оборудование для приготовления суспензии стабилизаторов в пластификаторе и высокоточные дозирующие устройства, позволяющие производить дозировку компонентов с точностью до 2 %.
2) Смеситель ПВХ-композиции.
3) Пластицирующая установка (двухшнековый или валковый экструдер или пластосмеситель).
4) Дополнительная пластицирующая установка, состоящая из одного или двух вальцов и «стрейнера».
5) 4-х- или 5-тивалковый каландры.
6) Послекаландровая линия, включающая:
6.1) съемное устройство;
6.2) устройство для термообработки пленки («отпуска» или «закалки»), которое называют еще «темперирующим устройством».
6.3) охлаждающее устройство;
6.4) намоточную группу (с компенсатором или без него);
6.5) тиснильную (сатинирующую) группу;
6.6) устройство так называемого «суперфиниша» (при изготовлении пленки с глянцевой зеркальной поверхностью).
7) Теплостанции валковых групп.
8) Процессор для управления технологическим процессом.
(Конструкторско-технологические особенности каландровых линий. Полименные материалы, №7, 2012).
Методом каландрования можно получать жесткие и пластифицированные ПВХ–пленки толщиной (80-800) мкм. Ширина пластифицированных мягких ПВХ пленок может доходить до 5,0 м.
Оборудования для изготовления стеклопластиков и углепластиков
Стеклопластики и углепластики изготавливают на основе тканых и нетканых волокнистых материалов и различных связующих.
При изготовлении стеклопластиков используется стеклоткань (стеклонити), при изготовлении углепластиков ткань или нити из углеродного волокна.
Стеклопластики и углепластики изготавливают следующими основными способами:
- контактный (при помощи резиновых мешков и эластичных пуансонов,
- метод аппликации (ручная оклейка),
- метод напыления,
- непрерывный метод, применяемый для изготовления цилиндрических изделий.
Оборудования для производства изделий из древопластиков
Основными изделиями, получаемыми из древопластиков, являются древесностружечные и древесноволокнистые плиты, профильные древесностружечные изделия.
Древесностружечные плиты формуют периодическим и непрерывным способом.
При периодическом способе производства используют гидравлические одноэтажные и многоэтажные прессы. Непрерывный способ производства реализуется на формующих машинах оснащенных ленточным прессом.
Древесноволокнистые плиты изготавливают мокрым и сухим способами.
При сухом способе волокнистая масса от машин, разделяющих щепу на волокно, до формующей машины транспортируется в воздушном потоке, а не в потоке воды.
Оборудование для пропитки и промазки
Пропиточные машины
Пропиточные машины применяются в основном при производстве слоистых пластиков для пропитки тканевой и бумажной волокнистой основ.
Пропиточные машины в зависимости от конструкции сушильной камеры подразделяются на туннельные, контактные и камерные; в зависимости от направления движения основы – на вертикальные и горизонтальные; по способу термообработки – с воздушной и радиационной сушкой.
Промазочные машины
Промазочные машины для нанесения паст ПВХ
Промазочные машины применяются для нанесения паст ПВХ-пластизоля на текстильную и другую основу с последующей желатинизацией, нанесением печатного рисунка и защитного покрытия.
На промазочных машинах изготавливают промазкой линолеум, а также декоративные ПВХ-материалы на бумажной и тканевой основе.
Производство ПВХ–материалов на основе пластизолей включает также оборудование для приготовления паст-пластизоля, а также пигментных паст.
Основными узлами установки (линии) для нанесения ПВХ-пластизолей являются:
- размоточное устройство для основы (ткани или бумаги);
- узел нанесения пасты (ракельный или валковый);
- желирующий канал — устройство для нанесения печатного рисунка;
- сушильный канал для сушки краски;
- тиснильное устройство;
- намоточное устройство.
Промазочные машины для нанесения клея (лака).
Промазочные машины для нанесения клея (лака) применяются для нанесения клеевого слоя или слоя лака на основу, в качестве которой используются полимерные пленки, ткани или бумага.
Нанесения клея (лака) может осуществляться ракельным и валковым способом.
Конструкция клеепромазательной машины (лакирующей машины) включает:
- размоточное устройство для основы (ткани или бумаги);
- узел нанесения клея (ракельный или валковый);
- сушильный канал;
- намоточное устройство.
Оборудование для производства синтетических ворсовых покрытий.
При производстве синтетические ворсовых покрытий могут быть использованы как нетканые ворсовые материалы, так и синтетические нити, которые сплетаются и механическим способом прикатываются к покрытию из ПВХ-пластизоля предварительно нанесенному на тканевую основу.
Другим способом получения ворсовых материалов является флокоулирование. При флокоулировании на текстильную ткань или бумагу наносится клеевой слой, после чего на клеевой слой наносят синтетические волокна (флоки). Флоки наносятся при помощи специального дозировочного устройства на сетчатый электрод с отрицательным зарядом.
Под текстильной или бумажной подкладкой находится заземленный положительный электрод. К системе подводится высокое напряжение 80-100 тыс В. В образующемся электростатическом поле волокна строго перпендикулярно опускаются в слой клея, после чего производится сушка и закрепление флоков на поверхности ткани или бумаги.
Оборудование для производства газонаполненных пластмасс
Газонаполненные пластмассы получают несколькими способами: автоклавным, беспрессовым, экструзионным, литьем под давлением и т.д. При производстве газонаполненных пластмасс используют принципы физического или химического вспенивания.
При физическом вспенивании образование начальных пузырей, которые, в последствии фиксируются в качестве пор, происходит за счет интенсивного смешивания массы полимера с воздухом или инертным по отношению к полимеру газом, в качестве таких газов используется, например пропан и изобутан.
При химическом вспенивании образование пузырей происходит при термическом разложении соединений, добавляемых в состав полимерных композиций-порофоров.
Получение газонаполненных пластмасс может производиться на тех же технологических линиях, что и «компактных» материалов, однако в ряде случаев они должны оснащаться специальным формующим инструментом и специализированными узлами.
Оборудование общего назначения
Машины для измельчения
Под измельчением понимается процесс разрушения кусков твердого материала до заданных размеров, необходимых для промышленного использования продукта измельчения.
Процесс измельчения разделяют на две стадии:
- Дробление
- Помол
В ряде случаев первой стадии, «дробления» бывает вполне достаточно для выполнения технологических задач в производстве того или другого вида полимерных материалов.
Таким задачами, например, являются дробление некондиционных продуктов производства, с последующим их возвратом в производственный цикл при литье, экструзии и каландровании широкого спектра полимерных материалов.
В результате дробления образуются частицы (куски, дробленка) с размерами (2-20) мм.
При «помоле» исходным материалом является продукт, образующийся при дроблении. В результате помола размер частиц конечного продукта составляет (0,1-0,3) мм.
Следует отметить, что помол применяется гораздо реже, чем дробление и используется в основном в процессах получения композиционных материалов, например ПВХ-композиций, порошка вулканизованной резины, а также в процессах получения различных полимерных смесей, в которых требуется хорошее распределение разнородных компонентов в процессе смешения.
Помол по сравнению с дроблением является гораздо более затратным процессом, в части как капитальных, так и эксплуатационных затрат.
Для дробления применяются механизмы называемые дробилками, которые по конструкции и принципу действия подразделяются на:
- Щековые
- Конусные
- Валковые
- Молотковые
- Бегуны.
Для помола используют мельницы. По конструкции и принципу действия различают следующие типы мельниц:
- Барабанные
- Ролико-маятниковые
- Молотковые
- Мельницы типа «Аэрофол»
- Вибрационные
- Струйные.
Машины для сортировки
В ряде случаев, при ведении технологического процесса переработки пластмасс на стадиях подготовки сырья и также при конечных операциях, например, при гранулировании необходимо отделении более мелких фракций от более крупных с целью получения частиц полимерного материала в пределах заданных размеров.
Существуют следующие способы сортировки материалов:
- механическая сепарация (грохочение)
- воздушная (сепарация)
- гидравлическая (классификация)
- электромагнитная сепарация.
Для механической сепарации применяют грохоты, которые подразделяют на плоские, с горизонтальным или наклонным расположением сит и барабанные, в которых сито имеет форму цилиндра или многогранной усеченной пирамиды.
Действие воздушных сепараторов основано на действие воздушных потоков на частицы определенного веса и размера, с учетом различных аэродинамических характеристик этих частиц.
Электромагнитные сепараторы используются для отделения частиц с металлическими включениями от основной массы сырья. Системы электромагнитной сепарации широко используются на производстве в различных технологических процессах в системах автоматической блокировки работы технологического оборудования, при попадании металлических частиц в бункера и валковые группы перерабатывающих машин (экструдеров, каландров).
Аппараты для очистки воздуха от газов и пыли
В результате работы по дроблению и помолу, а также при транспортировке полимерных материалов их загрузки и смешении образуются мелкие частицы в виде пыли, наличие, которой отрицательно сказывается на ход технологического процесса, а также приводит к запыленности производственных помещений и выбросам в окружающую среду.
Для очистки пылевоздушной и газовоздушной смеси применяют следующие методы очистки:
- Механическую сухую в центробежных циклонах
- с помощью матерчатых фильтров
- электрическую
- мокрую.
Большинство процессов переработки пластмасс сопровождаются тепловым воздействием на полимерные материалы, при котором происходит выделение улавливаемых паров и газов. Улавливание газов и паров может осуществляться в электрофильтрах, при этом степень очистки может доходить до 99,5%.
При мокрой очистке газы и пары улавливаются в результате сорбции соответствующим сорбентом. В ряде случаев сортированные пары и газы могут использоваться вторично после проведения процесса десорбции.
Затворы, питатели и дозаторы
Затворы предназначены для перекрытия выпускных отверстий из бункера при дозировании.
Основные требования, которым должен удовлетворять затвор:
- небольшое усилие для открывания и закрывания,
- незначительное время на закрывание и открывание,
- герметичность и невозможность самопроизвольного открытия,
- возможность регулирования выхода (потока) материала.
Различают клапанные, подпорные, шиберные и секторные затворы.
Питатели предназначены для непрерывной подачи полимерного материала в емкости, трубопроводы, бункера.
В зависимости от конструкции питатели делятся на: ленточные, лотковые, маятниковые, секторные, барабанные, дисковые, винтовые (шнековые).
Дозаторы предназначены для подачи материалов в технологический процесс в заданном количестве.
Как правило, операция дозировки материала предшествует смешению.
- По физическому принципу работы различают объемные и весовые дозаторы
- По виду работы дозаторы могут быть ручными и автоматическими
- По типу технологического процесса — непрерывного и периодического действия.
В основе конструкции объемных дозаторов всегда имеется элемент, который контролирует определенный объем порции загружаемого материала. Например, в объемном дозаторе периодического действия это бункер определенного объема, при заполнении которого происходит его выгрузка.
Работа объемного дозатора непрерывного действия может быть привязана к числу ходов поршня в цилиндре определенного объема или времени работы насоса определенной производительности.
Весовые дозаторы содержат элементы конструкции, которые способны определять массу дозируемого материала с достаточной степенью точности. Этими элементами являются рычажные механизмы (грузовые рычаги) или тензометрические датчики.
Машины для смешения материалов
Смешение — это процесс, при котором два или более компонента смешиваются в определенном соотношении до получения однородной смеси.
В зависимости от типа технологического процесса смешение может быть периодическим и непрерывным.
Смесители для жидких материалов используются для приготовления различных растворов, суспензий, эмульсий, а также для интефикации процессов тепло- и массообмена.
Смесители для жидких материалов подразделяются на: механические и пневматические, а механические — на лопастные, пропеллерные, турбинные и специальные.
Смесители для сыпучих материалов также могут быть периодического и непрерывного действия.
Конструктивно смесители периодического действия в зависимости от типа рабочего органа подразделяют на: смесительные барабаны, червячно-лопастные, плунжерные, ленточные, смесители центробежного действия, смесители бегуны.
Смесители для пластических (вязких) материалов, в зависимости от вязкости смешиваемых материалов, подразделяются на: лопастные, турбинные, ленточные, дисковые, гребенчатые, планетарные с вращающимся корпусом и лопастью (подвижной и неподвижной), якорные и рамные, с двойными лопастями (вращающиеся в противоположных направлениях), с вертикальным винтом, шаровые мельницы, валковые машины, смесительные бегуны, червячные и роторные.
Оборудование для транспортирования материалов
В ходе технологических процессов по переработке пластмасс необходимо осуществлять операции по перемещению сырья и материалов.
Эти операции осуществляются при помощи транспортирующих механизмов. Транспортирующие механизмы классифицируются в зависимости от типа движущей силы, которая перемещает груз.
По этому признаку они подразделяются на:
- конвейеры,
- пневмотранспортные установки
- гидротранспортные установки.
Конвейеры, по конструкции, подразделяют на:
- ленточные,
- пластинчатые,
- скребковые,
- ковшовые,
- скребково-ковшовые,
- люлечные,
- тележечные,
- грузоведущие,
- подвесные,
- штанговые,
- шагающие,
- эскалаторы,
- элеваторы,
- винтовые,
- качающиеся,
- роликовые с вращающиеся трубы.
Последние четыре типа конвейеров не имеют тягового элемента (лента, цепь, канат, штанга).
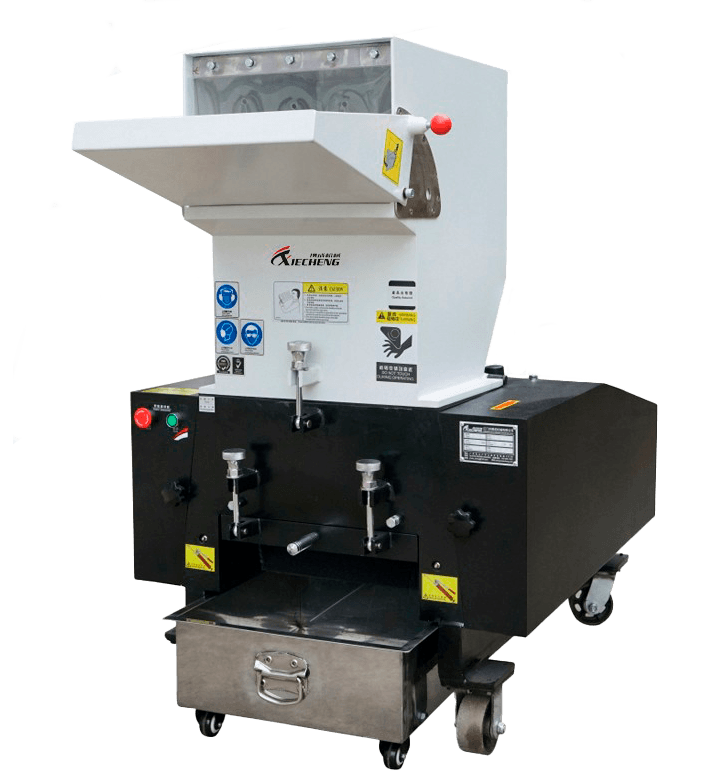
Вспомогательное оборудование для производства пластиковых изделий
Инструмент и оборудование для обработки и сварки пластмасс
Основным рабочим инструментом при формовании изделий из пластмасс методами прессования, литья под давлением, вакуумного, пневмо- и механического формования являются пресс-формы, методом экструзии экструзионные головки.
Пресс-формы
Их можно классифицировать по технологическим, эксплуатационным и конструктивным признакам.
По технологическому признаку пресс-формы делят на следующие:
- компрессионные
- литьевые, устанавливаемые на гидравлические прессы
- формы литья под давлением для термопластов, устаналиваемые на литьевые машины и формы для вакуумного и пневмоформования
- формы для механического формования.
По эксплуатационному признаку пресс-формы делят на съемные (снимаемые при извлечении изделий), полустационарные (извлекается только матрица) и стационарные (закрепленные в прессе или машине).
По конструкционному признаку пресс-формы делят на:
- компрессионные – открытого, полузакрытого и закрытого типа. Полузакрытого обратного типа с общей загрузочной камерой, с индивидуальными загрузочными камерами для каждой формующей полости, со встречными пуансонами;
- литьевые – с верхней загрузочной камерой и нижней загрузочной камерой;
- формы для литья под давлением с общим и раздельным впрыском;
- с автоматическим выдвижением формующих знаков или вывинчивания резьбовых знаков;
- с автоматической установкой арматуры;
- формы для вакуумного, пневмо- и механического формования — негативные и позитивные.
Все группы пресс-форм делят на одногнездовые и многогнездовые, а по характеру разъема матрицы –на пресс-формы с одной, двумя или несколькими горизонтальными плоскостями разъема (галетные), с одной или двумя вертикальными плоскостями разъема и с комбинированным разъемом.
Пресс-форма любого типа состоит из двух основных групп деталей: технологического и конструктивного назначения. К первой группе относятся рабочие детали, детали литниковой системы и загрузки, а также выталкивающие, установочные и детали перемены движения.
К рабочим деталям относятся: матрицы, пуансоны, формующие знаки, вставки, резьбовые знаки и кольца, то есть те детали, которые непосредственно соприкасаются с материалом и участвуют в придании изделию заданной формы.
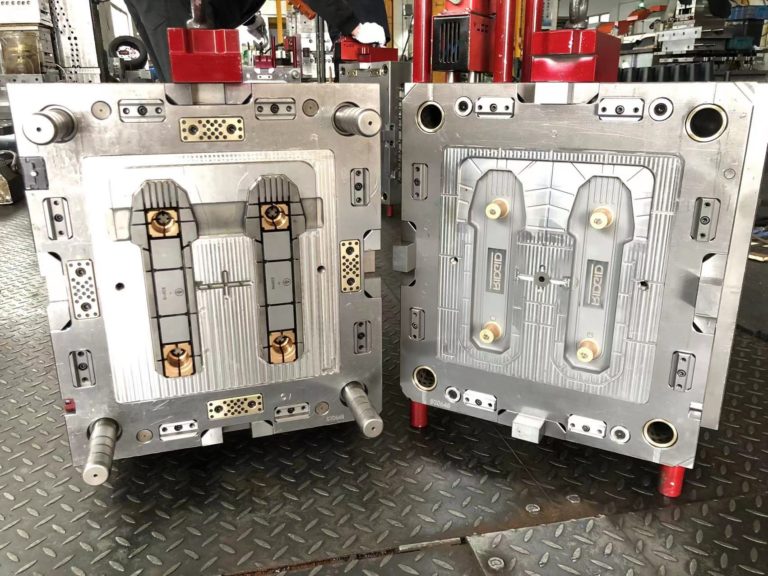
Пресс-формы для литья пластмасс
Экструзионные головки
Головки отличаются большим разнообразием типов и конструкций, которые могут быть классифицированы следующим образом.
По направлению выхода изделия:
- прямоточные головки с направлением выхода изделия вдоль оси червяка (головки для труб, шлангов, стержней.);
- угловые головки, осуществляющие поворот потока расплава и соответственно изменяющие направление выдачи изделия на определенный угол по отношению к оси червяка (головки для покрытия проводов, кабелей, и каких-либо сердечников изоляцией, головки для рукавной пленки, экструзии с раздувом).
Прямоточные головки просты по конструкции, условия течения расплава в их каналах максимально благоприятно. В связи с этим при выборе головки им следует отдавать предпочтение, однако в приведенных в пункте 2 примерах их использование невозможно.
По конфигурации формующей щели:
- плоскощелевые (для получения пленки и листа);
- головки с кольцевым поперечным сечением канала (головки для цилиндрических стержней, трубные головки, головки для экструзии с раздувом, для получения рукавной пленки);
- профильные головки, имеющие сложный контур поперечного сечения формующего канала и различающиеся по конфигурации поперечного сечения изделия на головки для изделий открытого типа, закрытого типа, смешанного типа, специальные головки и головки для изделий из вспененных материалов.
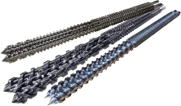
Запчасти и комплектующие
Оборудование для механической обработки изделий из пластмасс
Оборудование для дополнительной обработки изделий из пластмасс классифицируется на две основные группы:
- Станки и машины для резки листов, пленок, труб, плит, блоков и других заготовок; гильотинные и пресс-ножницы;циркуляционные и ленточные пилы; станки для резки абразивным кругом; строгальные машины и токарно-лущильные станки для получения листов и пленок из блоков и болванок.
- Станки для обработки отформованных изделий цикличными методами:галваточные барабаны, однооперационные станки, много операционные станки, станки для отделки, раструбовочные машины.
Оборудование для сварки пластмасс и нанесения пластмассовых покрытий
Оборудование для сварки пластмасс
Классифицируется на:
- оборудование для сварки нагретым воздухом;
- оборудование для сварки нагретым инструментом;
- оборудование для сварки горячим присадочным материалом;
- оборудование для сварки нагревом токами высокой частоты;
- оборудование для сварки с помощью инфракрасного излучения; оборудование для сварки трением;
- оборудование для сварки ультразвуком.
Установки для нанесения пластмассовых покрытий
Оборудование для нанесения пластмассовых покрытий классифицируют:
- в зависимости от условий образования взвешенного (кипящего) слоя — вихревой, вибрационный, вибровихревой;
- от способа нанесения порошка на изделие — струйный метод, распыление в электрическом поле, напыление в ионизированном кипящем слое,
- от способа оплавления порошка — теплолучевой, индукционный, газопламенный;
- от вида применяемой аппаратуры — камерные и бескамерные методы.
Заказать оборудование для переработки пластмасс
Команда Интерпласт подберет для вас оборудование от официальных поставщиков – заводов Китая. Напомним, что мы специализируемся на экструзионном, выдувном, литьевом и оборудовании для переработки и грануляции пластика. Оставьте заявку в форме ниже.