Технический аудит для полимерных производств: польза для производителя и пример анализа
Часто случается так, что находясь в процессе решения операционных задач владельцы предприятия могут не видеть объемы финансовых потерь и потенциальные возможности оптимизации производства. Для этого мы проводим, так называемый, производственный (технический) аудит, в котором соотносим затраты и производительность с прибылью, а также предлагаем наиболее рациональные пути увеличения рентабельности предприятия.
В этой статье мы расскажем про технический аудит на примере трубного производства и поделимся тем, к каким выводам мы приходим чаще всего и какие решения предлагаем для клиентов.
Кому это полезно
Обычно именно для экструзионных производств (трубы, листы, профиль) вопрос стоит более остро, так как линии собираются из разных узлов, и есть возможность модернизировать отдельные узлы.
Как правило, на литьевом производстве оптимизация достигается за счет усовершенствования/замены пресс-формы или внедрении вспомогательного оборудования для оптимизации процесса. Конечно, можно модернизировать термопластавтомат путем замены электроники и мотора, но обычно это нецелесообразно, и приобретение новой машины окупится куда быстрее и гарантированно. Важно помнить, что за производительность все равно отвечает литьевая машина.
Из чего состоит аудит
Аудит проводится техническими специалистами с опытом работы на полимерных производствах более 10 лет. Он состоит из оценки нескольких показателей и качественных характеристик. Впоследствии, это дает полную картину текущего производства и помогает оценить возможности для развития.
Важнейшими показателями для экструзионного производства являются:
- энергопотребление на 1 кг сырья
- производительность оборудования (кг/час).
Помимо этого специалист оценивает:
- состав оборудования (наличие периферийного оборудования, количество и длина ванн охлаждения, количество насосов в вакуумном танке, наличие отрезного устройства, а также, какие диаметры трубы могут производиться на данной линии)
- общее состояние оборудования (внешний вид, коррозия, мощность двигателя, стабильность давления в редукторе, степень устаревания)
- качество выдаваемого изделия (количество брака, соответствие изделия необходимым стандартам)
- качество сырья
- возможности автоматизации и модернизации
- эффективность процесса работы.
После сбора всей информации, мы сопоставляем, в первую очередь, потребление электроэнергии и производительность и делаем пересчет в рублях. Далее сравниваем с оборудованием, которое мы производим на заводе Neo-Ental (Шанхай).
Пример расчета и сравнительного анализа
Для примера возьмем сравнение двух экструзионных линий для производства труб с разными показателями.
Показатель |
Линия клиента,110-280 мм |
Линия Интерпласт, 110-315 мм |
Производительность (кг/час) |
260 |
500 |
Расход электроэнергии (кВт/кг) |
0,9 |
0,46 |
Расход электроэнергии в рублях на 1 кг сырья (стоимость электроэнергии 5,5 руб/кВт) |
0,9*5,5=4,95 |
0,46*5,5=2,53 |
Суточное потребление электроэнергии в рублях |
4,95*260*24=30 888 |
4,95*500*24=30 360 |
Производительность в сутки (т/сутки) |
6,2 |
12 |
Потери готовой продукции (в сравнении с линией «Интерпласт») - 174 тонны в месяц Потери в рублях на электроэнергии на действующей линии составляют (в сравнении с потребляемой электроэнергией с линией «Интерпласт») – 13 939 руб/сут. В месяц – 418 146 руб/мес. В год – 5 018 112 руб
Часто на производствах стоит не 1 линия, то есть переплата в 5 млн рублей в год возрастает в 2 и более раз. Поэтому обновив оборудование на высокоэффективное, клиент может платить в 2 раза меньше, а получать при этом в 2 раза больше изделия.
План модернизации
После расчета мы составляем план по модернизации или замене оборудования. Далее возможно несколько сценариев развития, и это зависит от бюджета клиента.
Ниже несколько примеров:
- Если постэкструзионное оборудование линии справляется с выпускаемым объемом, то можно заменить только экструдер, таким образом увеличить производительность и снизить энергопотребление. Это же работает и в обратную сторону.
- Однако если тянущее устройство не справляется или ванн охлаждения недостаточно, то, скорее всего, труба не успевает остывать. И в данном случае смысла ставить более мощный экструдер нет. В таком случае придется обновлять всю линию и подбирать комплект, который будет обеспечивать максимальную производительность на всех узлах.
- Есть же недостает отрезного устройства или какой-то периферии, то предлагаем автоматизировать процессы и исключить ручной труд при загрузке сырья и нарезке изделия.
В нашей практике наиболее часто встречающаяся проблема — это низкая производительность и высокие затраты на электроэнергию. Помимо оценки оборудования, мы готовы дать рекомендации по сырью и основным поставщикам и добавкам, чтобы повысить качество конечного изделия. А также по налаживанию производственных процессов.
Сколько занимает времени и в каком формате
Суммарно технический аудит занимает около 3-5 дней: 1-2 дня на осмотр производства и сбор данных, 2-3 дня на расчет и подготовку сравнительного анализа.
Мы подготавливаем всю информацию в виде подробного экономического обоснования и расчетом существующей и потенциальной рентабельности. После этого по запросу составляем коммерческое предложение.
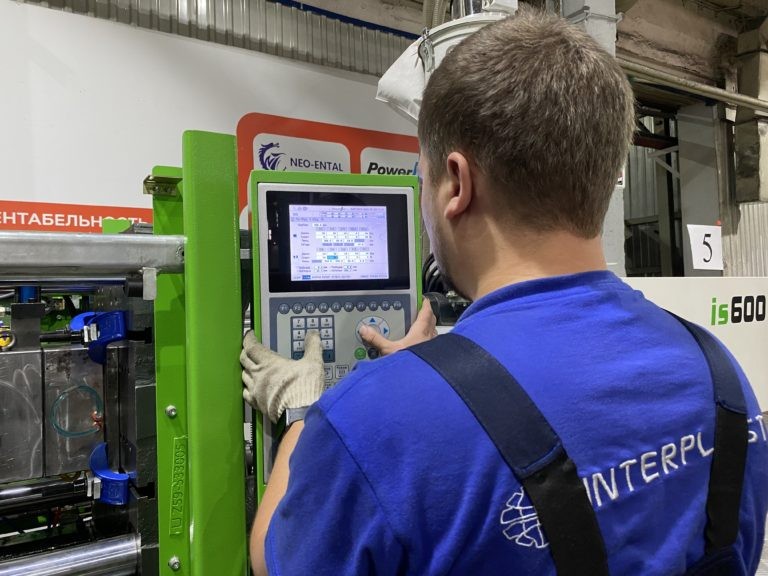
Технический аудит
Подытожим
В нашей практике уже несколько клиентов после аудита начали процесс обновления парка оборудования, потому как выгоды очевидны. Ведь часто модификации старого оборудования по итогу не окупаются, производительность остается на том же уровне, простои производства увеличиваются из-за частых ремонтов и рентабельность производства стремится к нулю, а то и в минус.
Если вы понимаете, что ваше оборудование устарело, но не можете самостоятельно расставить приоритеты по замене узлов и выбрать поставщика, аудит производства позволит в цифрах получить прозрачную картину на сегодняшний день и выстроить перспективу на будущее, обеспечив себе стабильное и системное развитие.