Двухшнековый экструдер для полимеров: что это такое, характеристика и как работает оборудование
Двухшнековые экструдеры для полимеров: что это такое
Наиболее сложная модель экструзионного оборудования состоит из двух взаимодействующих, одновременно вращающихся шнеков, установленных в цилиндре. Они различаются между собой по конструкции и режиму действия, что обеспечивает работу с широким спектром пластмасс разного агрегатного состояния.
Таблица 1. Типы используемого сырья
Разновидность материала | Форма |
---|---|
Поливинилхлорид | Порошок |
Полиэтилентерефталат | Гранула |
Полиэтилен низкого давления | Дробленый |
Красители | Жидкостные вещества |
Прочее |
Немного истории
Экструзионная технология зародилась в 30-е годы XX века. Производство начиналось на одношнековых устройствах. В 40-х гг. изобрели ПВХ, с которым имеющиеся машины не справлялись, что привело к закономерной их эволюции, разработке новых элементов и появлению двухшнековых экструдеров.
Они в своем развитии прошли большой путь и претерпели много трансформаций. Сейчас, по сути, принципиально ничего не меняется: механизм уже отработан не одним десятком лет. Улучшение идет в сторону снижения потребления энергии, повышения показателей эффективности смешения и производительности. Дорабатываются структуры стержней для лучшей обработки полимеров. Сложнее становится промышленная автоматизация, связанная с подготовкой сырья, его точным дозированием и регулировкой подачи, терморегуляцией. Это позволяет комбинировать несколько этапов технологического процесса в непрерывно работающей линии.
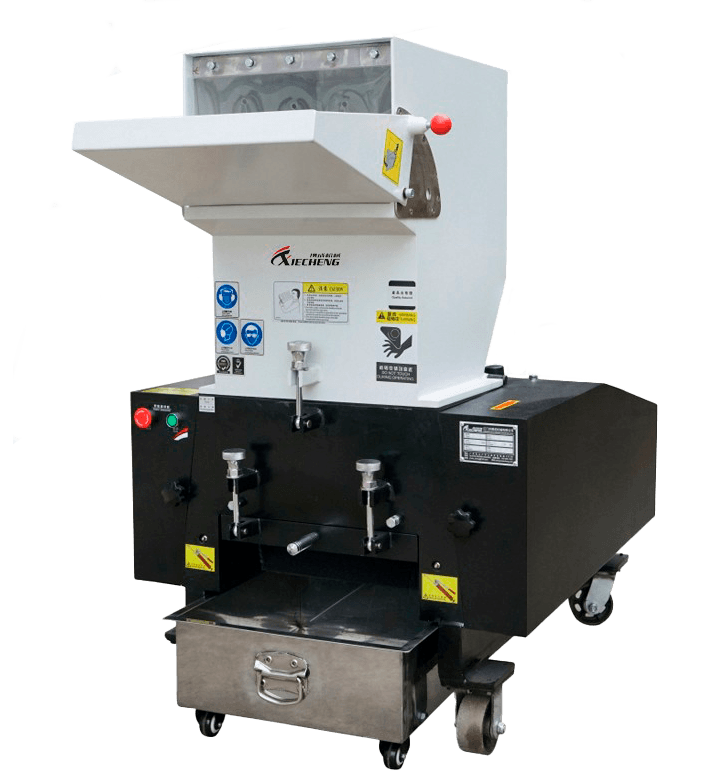
Вспомогательное оборудование для производства пластиковых изделий
Принцип работы двухшнекового экструдера
Транспортирование и пластикация внутри цилиндра происходят под действием шнековой пары. Захватывая материал, она перемещает его от загрузочной зоны к экструзионной голове для продавливания через фильеру. В результате масса сжимается, нагревается, приобретает вязкость и однородность.
Как правило, питание машины осуществляется из бункера, в который загружается сырье: потом оно поступает в нужный участок за счет естественного ссыпания (под действием силы тяжести). Нужный уровень регулируется автоматически открытием/закрытием шибера, которым оснащен бункер. Важным устройством в случае использования сыпучих веществ является шнековый дозатор, который обеспечивает равномерную подачу в сектор загрузки.
Чтобы понять иные нюансы того, как работает двухшнековый экструдер, посмотрите на изменения производительности в зависимости от размера комплектующих и потребляемой мощности двигателя (на примере характеристик оборудования в линейке «Интерпласт»).
Таблица 2. Рабочие параметры
Признак | Показания | |||||
---|---|---|---|---|---|---|
Модель, SJZ | 45/90 | 55/110 | 65/132 | 65/132В | 80/156 | 92/188 |
Мощность, кВт | 15 | 22 | 37 | 55 | 55 | 110 |
Диаметр концов шнека, мм | 45/90 | 55/110 | 65/132 | 65/132 | 80/156 | 92/188 |
Производительность, кг/ч (с учетом типа сырья и изделия) | 50-80 | 80-150 | 150-250 | 250-450 | 250-400 | 400-600 |
Сравнение оборудования с двумя и одним стержнем
При использовании пары шнеков значительно возрастает степень смешения и гомогенизации, снижаются энергозатраты. Дело в том, что вместе деталям легче проталкивать материал, поэтому мощности электрического двигателя могут быть ниже – это дает экономию энергопотребления.
Важно и то, что можно сразу дозировать полимер, добавки и красители. На выходе получать качественное изделие независимо от состава и агрегатного состояния исходных компонентов.
Однако при всех преимуществах экструдер с двумя рабочими элементами отличается более высокой стоимостью в сравнении с простыми моделями за счет усложнения структуры. Больше стержней, следовательно, увеличиваются габариты цилиндра, ставятся дополнительные нагреватели.
Таблица 3. Плюсы и минусы аппаратов
Одношнековый | Двухшнековый |
---|---|
Пластикация одного вида термопласта | Обрабатывает высоконаполненные и чувствительные к повышенным температурам материалы. Совмещает операции смешивания компонентов |
Экструдирует гранулированный и дробленый пластик | Широкий диапазон частиц: от мелкого порошка до гранул и дробленки; жидкие компоненты в полимерных смесях |
Удовлетворительные характеристики пластикации | Значительная перемешивающая и гомогенизирующая способность |
Повышенное энергопотребление относительно конических с двумя стержнями | Эффективное использование энергии |
Простая конструкция, ниже затраты на приобретение | Цена сравнительно выше из-за более сложного механизма, что компенсируется меньшими эксплуатационными расходами |
Применение двухшнековых экструдеров
Это базовые агрегаты во многих процессах получения пластиковых изделий благодаря хорошим характеристикам диспергирования и плавления. Оснащены различными шнеками и вспомогательными устройствами. Могут производить трубы малого и большого диаметра, всевозможные профили для окон, подоконников и дверей, ДПК доски, изоляционные кабели, пленку, листы и другие погонажные формы.
В ряде случаев их применению нет альтернативы. Например, если требуется использование веществ с малой насыпной плотностью или/и хорошая дегазация, компаундирование, грануляция и т. д. В то же время это специальный механизм для формования жесткого ПВХ и древесно-полимерного композита.
В сравнении с традиционным одношнековым оборудованием, которое может эффективно перерабатывать материалы с объемной массой не менее 500 кг/куб. м, двухшнековое способно проводить пластикацию веществ со свойствами не меньше 280 кг/куб. м.
Дегазация в экструдерах с двумя шнеками
Как правило, на третьем-четвертом участке цилиндра (где особенно интенсивный нагрев) устанавливается вытяжка с вакуумным насосом. Ее назначение в том, чтобы максимально удалить из расплава влагу, газообразные включения и захваченный воздух.
Особенность системы заключается в наличии изоляционного кожуха, который надевается на атмосферную зону. Втягиваемые насосом посторонние включения выводятся в емкость, потом утилизируются.
Если этого не сделать, то, например, при грануляции и работе со вторичкой возможны выбросы токсических веществ в цех, что небезопасно для здоровья сотрудников. И, конечно, страдают свойства продукции.
В ряде случаев хорошая вакуумная дегазация становится главным условием качества технологического процесса, а также самой возможности его проведения.
Виды и типы двухшнековых экструдеров
Характеристики оборудования касаются в первую очередь профиля шнеков: их конфигурации, направленности и частоты вращения. Также заметим, что для экструзии с более низкой производительностью обычно используются стержни с меньшими диаметрами концов. При этом они считаются экономичным выбором из-за энергосберегающих свойств.
По конструкции
В зависимости от формы и положения деталей относительно друг друга выделяют следующие их категории:
- параллельный и конический;
- с постоянной и переменной глубиной нарезки.
Уникальной особенностью конусовидного блока становится низкая скорость шнека, которая дает меньшие сдвиговые напряжения на материал. Это проверенная технология, означает небольшое повышение температуры без риска деструкции полимера. Мягкий эффект особенно важен в изготовлении продукции из порошкообразного сырья с низкой термостабильностью, такого как поливинилхлорид.
В параллельных часто используется модульное устройство, при котором стержень состоит из нескольких элементов. Благодаря чему, путем подбора и установки различных модулей, можно регулировать степень сжатия, размеры зон дегазации и интенсивность смешения. Кроме того, легко поменять износившиеся сегменты, и это будет дешевле, нежели обновлять целую деталь.
Схемы расположения стержней в двухшнековом экструдере:
По направлению вращения
Действие смесительных элементов в цилиндре может быть обращено как в одну сторону, так и в противоположные. По этому признаку разделяют устройства с сонаправленным и встречным кручением.
По режиму вращения
Движение шнекам задает электродвигатель. От того, насколько быстро это происходит, выделяют следующие варианты:
- низкоскоростное — до 200 об/мин;
- высокоскоростное — от 200 об/мин.
Конические вращаются медленнее, но это оправдано в производстве труб и профильных изделий при использовании порошка, поскольку они дают меньше тепла. Например, для экструзии ПВХ достаточно 55-37 об/мин, чтобы получать 150-450 кг продукции в час и при этом экономить на электропотреблении. Поэтому это не просто машина, а решение для оптимизации технологического процесса.
В параллельных обеспечивается работа на больших скоростях, что используется в основном при формовании ПЭТ-листов и компаунда, то есть смеси пластика с добавками и наполнителями. Альтернативный вариант здесь неприменим.
Примеры в производстве
Например, в работе с ПВХ и его композициями преимущественно прибегают к низкоскоростным экструдерам встречного вращения. Это обеспечивает щадящую обработку, которая необходима при чувствительности термопласта к нагреву и сильному сдвигу. Скорость крутящего момента зачастую не превышает 100 об/мин.
В случае применения конических шнеков насос расплава можно исключить из оснастки, что значительно снижает стоимость установки. Кроме того, в силу низкой термостабильности поливинилхлорида при его переработке не эксплуатируют насосы расплава, что также дает преимущество. В зависимости от размеров комплектующих, мощности двигателя и задач технологического процесса производительность может достигать 11 000 кг/сутки и более.
Параллельные экструдеры самые дорогие среди моделей с двойным винтовым механизмом. Используются, как правило, в линиях компаундирования. Имеют высокие показатели смешивания за счет действия узла на скорости в 300-500 и более оборотов в минуту.
Подведем итоги
Производство изделий из пластика в значительной степени зависит от двухшнековой экструзии. В частности, это касается выпуска из ПВХ труб малого и большого диаметра, крупных строительных панелей и мелких декоративных профилей.
Одна из особенностей оборудования — возможность подобрать конструкцию, размер и сдвиговое усилие шнеков под перерабатываемый полимер и производственный план с учетом всех технологических и экономических факторов. Тенденции развития направлены на повышенную скорость и низкое потребление энергии.
«Интерпласт» специализируется на поставках двухшнековых экструдеров с коническим механизмом для новых и модернизируемых линий. Под любые цели можно подобрать комплектующие, запчасти и периферию. Например, экструзионную фильеру, шнековую пару, системы дозирования и охлаждения, маркираторы и намотчики.
Чтобы вы не установили, следует помнить — срок службы оборудования в среднем составляет 10-15 лет. Со временем оно станет неэффективным по энергопотреблению, а продукция просто перестанет быть конкурентоспособной из-за высокой себестоимости. Поэтому нужно своевременно озадачиваться модернизаций, а еще лучше изыскать возможность проведения диагностики.
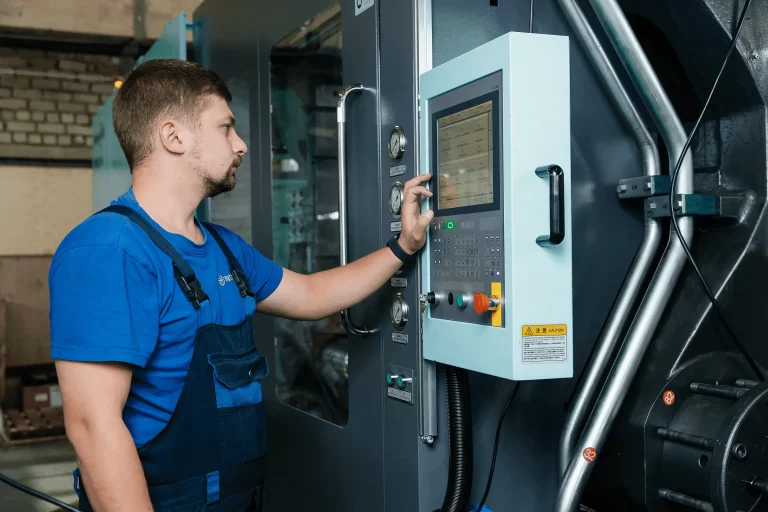
Диагностика оборудования для полимерных производств
Предприятия могут работать практически с любым пластиком, выбрав подходящую машину. Исключительно ими комплектуются линии для производства профильных изделий, труб из поливинилхлорида и товаров из древесно-полимерного композита. Применимо как первичное, так и вторичное сырье.
Самое важное — тип и агрегатное состояние материала, планируемая производительность. Подбор рабочих узлов, не соответствующих задачам предприятия, приведет к некачественной экструзии. Либо качество будет получено, но придется очень долго настраивать рабочие режимы: правильные температуры, обороты, давление и т. д. Чтобы убрать с себя ненужную нагрузку, лучше изначально поговорить с химиком-технологом и разработать рецептуру, грамотно составить техническое задание на сборку узлов, прописать требования к контролю.
По опыту нашей практики востребованы двухшнековые модели в экструзионных линиях для труб и профилей из ПВХ, а также изделий из ДПК. Запросы поступают как от производителей, так и от строительных организаций, которые стремятся наладить выпуск собственной продукции.