Выдув ПЭТ-тары: оборудование для производства пластиковых изделий
Мы давно работаем с предприятиями полимерной отрасли, сами производим изделия из пластика и можем с уверенностью сказать, что выдувная машина не столь сложна технологически, в эксплуатации и обслуживании, как, например, экструзионно-выдувные или термопластавтоматы. Но она способна стать фактором роста и капитализации бизнеса, позволит стабилизировать качество работы, а также независимо от поставщиков осуществлять бесперебойное обеспечение производственной деятельности упаковкой, имея запасы на складе в необходимом объеме.
Что значит выдув пластиковой ПЭТ-тары
Это способ получения полых емкостей из термопластика, который чаще всего идет в два этапа. Сначала полимерное сырье отливают в преформу на термопластавтомате (ТПА), а затем ее как воздушный шарик увеличивают в растягивающе-выдувной машине (РВМ), в результате чего получается полноразмерный сосуд.
Так производят бутылки, банки, флаконы для расфасовки жидкой и сыпучей продукции в пищевом, косметическом, парфюмерном, фармакологическом, химическом секторах промышленности.
Полиэтилентерефталат (PET) — это то, из чего выдувают ПЭТ-тару. Прозрачность, легкость, прочность, качественное и недорогое формование, вариативность форм и дизайна, возможность вторичной переработки — основные характеристики данного полиэфира, которые на рынке упаковки являются ключевыми аргументами в производстве и продажах.
Надо отметить, что существуют альтернативные варианты изготовления емкостей на одном виде оборудования — инжекционно-выдувном, это так называемая моностадия, которая объединяет литье заготовок и выдувание до окончательных размеров. Но для массового выпуска, когда речь идет о многомиллионных тиражах, традиционный вариант работы в два этапа, о котором говорим выше, будет эффективнее, потому что каждая стадия более специализирована и на огромных партиях работает быстрее и эффективнее.
Особенности выдува
Процесс имеет тонкую связь с назначением и размерами формуемого изделия. И чтобы правильно подобрать машину, необходимо проанализировать возможности оборудования, которое предлагает поставщик, и его соответствие вашим задачам.
Все, кто когда-либо изучал спецификации выдувных формовщиков, сталкивались с ограничением — на одном агрегате нельзя делать, например, обычные питьевые бутылки с узким горлом 28 мм и широкогорлые банки диаметром 60-100 мм. И вот здесь нужно подчеркнуть два важных момента.
Во-первых, для разных типов заготовок предусмотрены свои размеры конвейерных гнезд, на которые они ставятся.
Во-вторых, параметры будущего изделия влияют на габариты пресс-формы и пространство под нее внутри всего механизма. Поэтому нельзя просто взять и поменять компактную оснастку на большую.
Преформа как ключевое звено технологии выдува ПЭТ-тары
Заготовка — это отправной пункт будущей упаковки. Она сразу задает резьбу, высоту и диаметр горловины. Это наиболее критичный фрагмент с точки зрения обработки, который не должен меняться в процессе формования. Нагревание и недостаточное охлаждение этой части приведет к изменениям формы, что означает невозможность навинчивания крышки, нарушение герметичности и проблемы с внешним видом. А это уже брак.
Кроме того, качество готового изделия зависит от свойств преформы. Из заготовки с дефектами кондиционной продукции не получить. Поэтому наличие царапин, помутнений, отклонений в закупорочной зоне, пузырьков воздуха и повреждений поверхности недопустимо.
Как выдуть ПЭТ-тару: описание этапов
Технологические действия разделены на подготовку и формование, которое включает растяжение-выдувание. Это разные функции, но они должны быть хорошо согласованы, чтобы создать равномерное распределение материала и качество изготовления.
Загрузка преформ
При работе на полуавтоматической машине работник руками берет заготовку и устанавливает ее на конвейер станции разогрева, попросту печи.
В автоматическом режиме задействован загрузочный бункер, основная задача которого — временное накопление и дозированная подача форм на ленту. Тут они сначала позиционируются вниз дном и в вертикальном положении продолжают движение. А уже перед печью подхватываются за горловину вилочным роботом, который их переворачивает и ставит на удерживающие штыри линии станции. Загрузка достаточно простая, несмотря на действие нескольких механизмов.
Обращайте внимание на совместимость подачи, разогрева и выдува: они должны идти одновременно и с одинаковой скоростью. При исправной и корректной работе всех узлов качество товаров стабильнее.
Разогрев до заданной температуры
Далее пластиковую заготовку нагревают, чтобы сделать ее более пластичной и пригодной для формования. Процесс протекает довольно мягко, чтобы избежать перегрева, иначе изделие деформируется и можно вовсе не получить нужную продукцию.
Для обеспечения температурной безопасности и неизменности горловой части используются инфракрасные лампы: они равномерно распределяют тепло только по поверхности преформы. В то время как индукционные, медные, керамические нагреватели греют все вокруг себя, что приводит к потере тепла и росту энергопотребления. Но главное, горячий воздух постепенно начнет нагревать элементы, которые охлаждают и держат горловину, что, безусловно, даст брак.
На коротких системах может стоять 20 ламп, на длинных вдвое больше. И если одна из них перегорит, то заменить ее можно без нарушений технологии. Специальные датчики оценивают температурный профиль. Хитрость производственного способа как раз в том, что форма равномерно прогревается на всю толщину. Если в работу идет преформа холодная внутри, но теплая снаружи, то ее будет не раздуть, а в худшем случае она просто разрушится.
Выдув и вытягивание
Разогретую заготовку перемещают в пресс-форму. Для придания полноразмерного профиля используется система подачи воздуха высокого давления и механический растягивающий стержень.
Сжатые воздушные потоки подаются до тех пор, пока преформа не коснется стенок формующих полостей, и поддерживается до ее остывания. Шток вставляется в горловину, он начинает постепенно двигаться и растягивать изделие в сторону донной части. Поскольку дно более толстое и само по себе не растянется так же быстро, как давление воздуха распирает более тонкие стенки, ему нужно немного помочь.
Выдувания без растяжения невозможно и следует контролировать соотношение их силы воздействия на материал. Важно добиться равномерной толщины. А это возможно, когда расширения заготовки вверх и в стороны синхронизированы и идут с одинаковой скоростью. Именно так делают хорошие пластиковые тары.
Охлаждение
Остывает изделие на холодных полостях пресс-формы, необходимую температуру поддерживает чиллер. После того как расширенный пластик «отдохнет», система откроется и емкость выйдет наружу. Ее примет оператор или вилочный робот и отправит либо на конвейер для транспортировки к разливной линии, либо в большую коробку, которая собирает готовые работы.
Технологический процесс можно расширить и организовать внутри разливного/фасовочного цеха выпуск не только собственных сосудов, но и заготовок для них. «Интерпласт» организует поставку установки выдува в комплексе с ТПА для литья преформ.
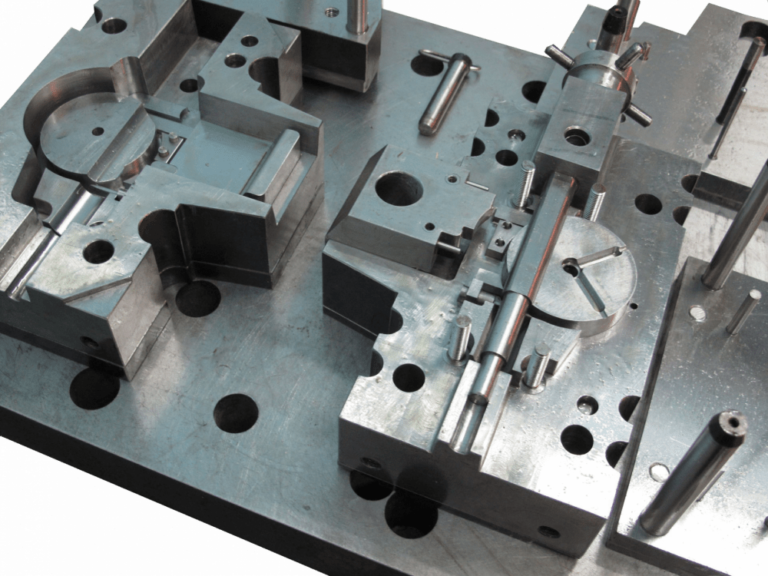
Пресс-формы для литья пластиковых изделий
Оборудование для изготовления пластиковой тары
Прежде чем начинать проект, необходимо определиться с технопарком, который вы будете использовать. Рассмотрим оснащение на примере двухстадийного производства, для организации которого потребуются литьевая и выдувная машины.
Термопластавтоматы для получения преформ
Изначально следует принять тот факт, что полиэтилентерефталат — очень текучий и чувствительный к перепадам температур материал. При перегреве он начнет желтеть и пригорать, на выходе получится бракованный товар недостаточной прозрачности или неправильного цвета. Поэтому работать с ним на стандартном ТПА не получится, нужен специализированный. Рассмотрим особенности наших спецсерий.
- PET — для высокоскоростного литья изделий из полиэтилентерефталата
В первую очередь выделим специально разработанную конструкцию шнека, которая позволяет повысить скорость и при этом снизить температуру пластикации, а значит, более эффективно перерабатывать полимер и улучшить качество товара.
Второе отличие — это применение максимально энергосберегающих технологий. Среди них регулируемая система управления насосом, которая уменьшает расход до 30% на впрыске и в процессе пластикации. А также серводвигатели для открытия/закрытия пресс-формы и выталкивания готовых изделий, которые дают экономию до 50% по сравнению с гидравлическими устройствами. На самом деле, при довольно коротких циклах и больших объемах продукции, которые получают производители, эти цифры в течение года становятся колоссальными.
- KPET — для скоростного литья преформ
Данная модель еще более оптимизирована под работу с упаковочным сырьем и, в частности, для выпуска форм до 20-25 г. Главные результаты, которых достигли разработчики, следующие:
- Производственный цикл уменьшен на 3-5 секунд в зависимости от конкретного изделия. Для этого синхронизирован процесс пластикации с открытием и закрытием пресс-формы. По нашему опыту, эксперименты уже проводились, в сопоставлении со стандартной серией PET на конкретных экземплярах можно получить экономию времени до 20-25%.
- Реализована система управления горячим каналом и контроль прозрачности дна заготовок, что облегчает деятельность операторов, а главное, минимизирует брак.
- Часто в качестве дополнительной функции ставят электрический узел впрыска, что позволяет дополнительно снизить расход энергии и сделать повторяемость впрыска более точной. Это сбережет материал и даст более качественное изделие.
Специалисты нашего завода-изготовителя PowerJet соотнесли показатели работы оборудования. Как видно из таблицы, на системе KPET время производственного цикла короче примерно на четверть. Что выгодно и с точки зрения снижения расходов на электричество, и со стороны оптимизации места в цеху. Собственно говоря, на тех же площадях можно выпускать гораздо больше продукции, завоевать большую долю рынка и получать сверхприбыль.
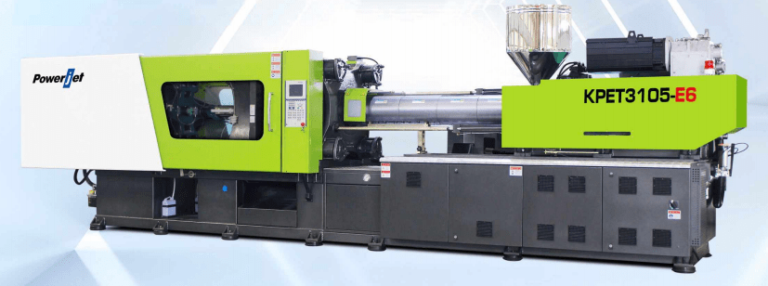
ТПА для литья преформ 8000-V6/S6 (серия PET)
Автоматы и полуавтоматы для выдува ПЭТ-тары
Оборудование, для которого входным сырьем служат преформы, а результатом обработки — полые прозрачные емкости, бывает двух видов: полуавтоматическое и автоматическое.
Первый тип эксплуатируют в условиях мелкосерийного выпуска, он зависим от ручного труда. Перед каждым новым циклом рабочий загружает необходимое количество заготовок на станцию разогрева, затем их вынимает и помещает в приемные формующие гнезда, снимает готовые изделия. Полуавтоматы не могут быть быстрыми, тут все зависит от опыта персонала, что ограничивает производительность не более чем несколькими сотнями единиц продукции в час.
Автоматические линии по производству пластиковой тары позволяют получать промышленные партии товара за короткий промежуток времени. Производителей привлекает высокая скорость, точность позиционирования и формования, возможность установки пресс-форм с гнездностью до 100 и более мест, а также высокая вероятность максимизировать прибыль и повысить продуктивность бизнеса.
Дополнительное оснащение
При изготовлении прозрачной полой упаковки из пластика используются единичные вспомогательные узлы, в частности:
- система подачи заготовок;
- компрессоры, которые вырабатывают сжатый воздух;
- чиллер для постоянного охлаждения пресс-формы;
- компьютерное управление.
Роботы в оборудовании для выдува ПЭТ-тары — часть машины, равно как загрузочный бункер с конвейером составляют единое целое.
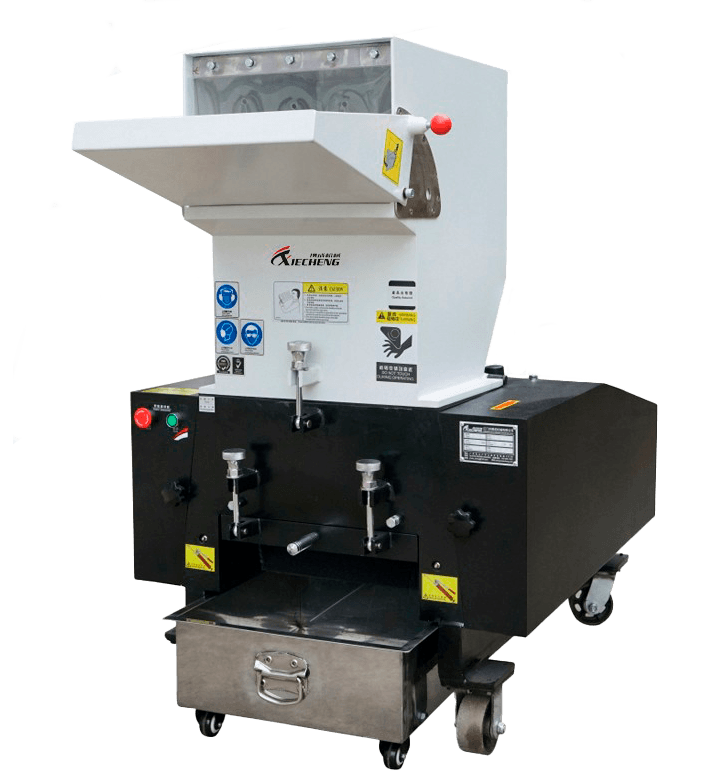
Вспомогательное оборудование для производства пластиковых изделий
Подведем итоги
Индустрия выдувного формования кардинально отличается от других направлений переработки пластика. Как правило, производством преформ занимаются одни компании, а изготовлением изделий из них другие. Покупателями РВМ-оборудования чаще становятся либо предприятия, которые нуждаются в сосудах для розлива и фасовки собственной продукции, либо небольшие предприниматели, которые, например, обслуживают сети магазинов разливных напитков и поставляют им емкости. Впрочем, есть и те, кто не занимается только закупкой заготовок, а объединяет оба процесса под одной крышей.
Специализированные машины чаще всего используются для изготовления емкостей размером от 50 мл до 19 л, будь то упаковка лекарств, косметических средств и парфюмерии, напитков и продуктов, детские бутылочки или резервуары для хранения авто- и бытовой химии.
Технологический парк составляют в соответствии с задачами бизнеса. Отталкиваются от типа изделия и потребностей в производственных мощностях. В своей практике мы сталкивались с тем, что конкуренты предлагали клиенту технику, не приспособленную для выпуска его продукции. А именно продавали машину с короткой станцией разогрева для работы с толстостенной заготовкой, которая на деле не успевала бы прогреваться и становилась непригодной для формования.
Это безальтернативный способ производства конкретного массового однотипного продукта — прозрачной полой тары. Поскольку ПЭТ обладает рядом преимуществ, не свойственных другим полимерам, его применение в упаковке для пищевых продуктов, бытовой химии и так далее оказывается все более обширным. И для многих предприятий выгодно иметь выдувную машину.