Чтобы оборудование поместилось в производственный цех: как мы «урезаем» дорогие экструзионные линии на 10 метров и более
На чем зарабатывает клиент
Это крупный телекоммуникационный и ИТ-холдинг, который контролирует значительное количество компаний, занятых в телеком-бизнесе и цифровых сервисах, а также в строительстве локальных и глобальных магистралей связи, требующих укладки гладких труб для защиты кабеля.
Цель — инвестировать в трубный рынок и перейти на трубы собственного производства. По оценке экспертов группы, это обеспечит независимость от сторонних подрядчиков и повысит надежность оснащения строительных объектов, позволит сохранить свою маржинальность. Плюс откроет новые перспективы для развития без риска недостаточного объема сбыта.
Обоснование решения «производить или покупать»
Клиент закупал трубы на стороне. Строительные объекты локализованы на северо-западе нашей страны. Предприятие успешное и прибыльное, но с ростом потребностей в долгосрочной перспективе могло столкнуться с серьезными проблемами. И основная из них — не исполнение контрактов, если у существующего подрядчика возникнут какие-то сбои, либо он поднимет цены существенно выше рыночных на фоне ажиотажа в высокий строительный сезон. К сожалению, подобные ситуации продиктованы самим рынком и стали нежелательными тенденциями для потребителей пластиковых труб.
Проанализировав ситуацию в трубной отрасли в России и свои нужды, руководство компании задумало построить завод по выпуску пластиковых труб в Архангельске. Сокращение необоснованных расходов и минимизация рисков в строительстве стали приоритетами.
Выбор оборудования для оснащения завода
Действие кейса разворачивается в сентябре 2022 года. Перед нами была поставлена задача подобрать и ввести в эксплуатацию экструзионную трубную линию, готовую к работе. У клиента не было опыта в полимерном производстве, и для него была крайне необходима экспертиза и комплексное сопровождение.
Отправными точками для составления технического задания стали лишь два параметра:
- материал — трубный полиэтилен низкого давления марки ПЭНД-100 в гранулах;
- широкий диапазон диаметров трубы — от 63 до 250 мм.
И наши специалисты, и руководство компании-заказчика понимали, что пока не удастся определить пул оборудования и требования к помещению под него, приступать к реализации проекта нецелесообразно. И поработать над этим нужно с помощью хорошей команды. Именно поэтому первым большим шагом в развертывании технического задания стали очные переговоры широким кругом участников с обеих сторон.
Преодоление ограниченного пространства
Клиент рассчитывал получить экструзионную линию с хорошими техническими и производственными показателями, с автоматическим уровнем настроек и мониторинга на русском языке, и разместиться в имеющемся помещении, которое оказалось мало под стандартную трубную линию протяженностью 53 метра. Тут мы сделали второй решительный шаг и выбрали нетривиальный подход к организации производства: сформировали линию с усеченными размерами и количеством некоторых узлов.
Комплект оборудования — 14 единиц, в том числе:
- вакуумный загрузчик
- гравиметрический дозатор
- одношнековый экструдер SJ65/38 для трубы ПЭНД
- одношнековый экструдер SJ25/25 для маркировочной полосы
- головка с матрицей
- вакуумный калибровочный танк
- ванна охлаждения
- четырехгусеничное тянущее устройство
- бесстружковое режущее устройство
- намотчик
- укладчик
- чиллер и другие вспомогательное узлы
Как добивались экономии пространства и сократили длину линии на 11 метров
- Уменьшили габариты вакуумного танка, который отвечает за калибровку изделия, с 11 до 9 метров, выиграв два метра площади.
- Убрали из комплекта одну из двух ванн охлаждения и высвободили еще девять метров. Да, потребуется немного больше времени для охлаждения трубы, но клиент принял это решение в пользу общей вместимости.
Достигнутое соглашение отвечает взаимной заинтересованности: со стороны клиента — в возможности в имеющемся помещении производить продукт с высокой маржинальностью и качеством, для компании «Интерпласт» — разместить оборудование с учетом эргономики пространства и сохранности производительности и свойств продукции.
Почему нельзя применить другое техническое решение
- Загнуть невозможно. При работе линии очень важна ось экструзии и по этой оси выставляется все оборудование, начиная от экструзионной головки и заканчивая укладчиком или намотчиком. Изгиб этой линии не допускается, возможно лишь небольшое отклонение от оси, которое не будет влиять на процесс экструзии.
- Выводить из цеха не имеет смысла. Все оборудование должно стоять в помещении при температуре не ниже +17 °C — это общее промышленное требование. Теоретически за пределы можно вынести укладчики, если сделать выход на улицу, но тогда труба будет забирать воздух именно с улицы — летом горячий и зимой холодный, что негативно скажется на технологическом процессе, потребует постоянных корректировок рабочих параметров и отразится на качестве.
Однако площадь, требуемая для расстановки оборудования — это далеко не все.
Насущная потребность каждой экструзионной линии — инженерные коммуникации: электроснабжение, водоснабжение и сжатый воздух. И тут одна из основных сложностей — подвести воду для охлаждения рабочих узлов и трубы. Для этого необходимо заглубить резервуар под воду объемом порядка 10 м3. На входе вода должны быть порядка +14 °C, в процессе работы экструдера она нагревается и уходит с линии 50-градусной. Диапазон регулирования и точность контроля за температурой возлагается на чиллер. В рамках рассматриваемого проекта емкость и водоотведение не были предусмотрены, вопрос пришлось решать заказчику фактически параллельно с приемом оборудования.
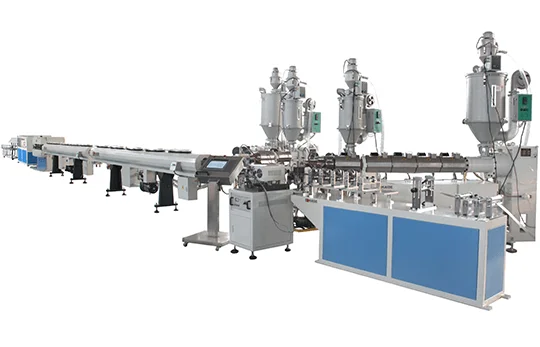
Экструзионные линии для производства труб
Производственные мощности
Сразу изготовили трехслойную экструзионную головку, которая применима для выпуска и однослойной, и многослойной трубы. Поэтому пропускная способность линии рассчитана на повышение общей производительности и выпуск новой функциональной продукции.
При этом одношнековый экструдер серии SJ65/38 может работать на высоких оборотах до 1500 об/мин, и таким образом достичь высокой производительности от 3 950 до 7 200 кг/сутки в зависимости от вида трубы.
Технологический запуск
- Установка — 9 дней.
- Тестирование на холостом ходу — 1 день.
- Тестирование производительности и качества продукции — 4 дня.
- Инструктаж операторов — 1 день.
Чтобы показать, что наше оборудование справляется с заданными типоразмерами, наладчики проводили испытания труб SDR 11, 13.6, 17 и 21 по одному диаметру с определенной толщиной стенок. Качество продукции соответствовало требованиям.
Однако не сразу расплав получился нужной консистенции. Дело в том, что первичные испытания проходили на заводе в Китае на местном сырье при достаточно высоких температурах. Заказчик оборудования использует полимер российского производства, который работает при другом нагреве. А поскольку на машине выставлены заводские параметры, в результате первого прогона линии показатели текучести трубного материала не дотягивали до нормы, а синий краситель для маркировочной полосы и вовсе давал очень жидкую полосу. Только после снижения температуры в обоих экструдерах, для красителя на целых 20 градусов, удалось получить нужную вязкость.
При запуске также обнаружили, что одна из гусениц тянущего устройства не движется. Причина банальная — выпала шпонка, видимо в процессе транспортировки ослабилась посадка детали, и она отпала. Наладчик поставил ее на место, крутящий механизм заработал. Важно отметить, что ослабление резьбового крепежа — не поломка, просто надо подтянуть и все будет работать.
Монтаж и пусконаладочные работы требуют много времени и знаний, прежде чем оборудование заработает правильно и безопасно. В связи с важностью работ следует нанимать только квалифицированных наладчиков, которые знают экструзионную линию и технологические режимы, а значит, все могут сделать правильно. Без такой поддержки очень сложно наладить выпуск трубы.
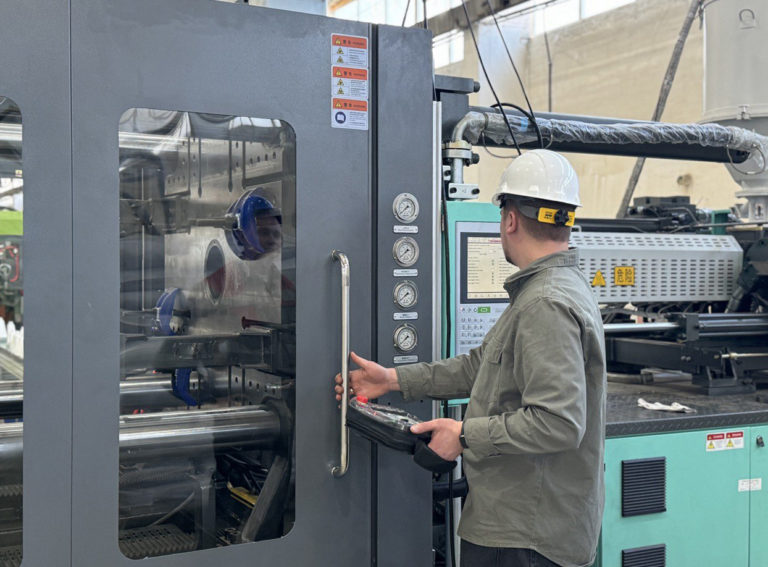
Монтаж и пусконаладка оборудования для полимерных производств
Перспективы
Завод рассчитывает обеспечивать строительные объекты холдинга не только однослойными трубами, но и многослойными; использовать мощности дополнительных экструзионных линий; решить задачу технического обслуживания в постгарантийный период и строгого контроля работоспособности; выводить товар на рынок.
Для начала предстоит освоить выпуск гладких однослойных труб и реализовать первый продовольственный план, затем охватить другие виды продукции и выставлять продукцию на продажу.
Заключение
В таких кейсах очень важен пример положительных результатов. Заказчики, даже с крупными бюджетами, зачастую обращаются с запросами на оборудование без какого-либо технического задания. Но пока у производственного проекта есть сильная техническая команда, работа идет на уровне нюансов и деталей, нерешаемых проблем не возникает, а бизнес становится рентабельным и конкурентоспособным. Все возможности первой трубной линии предполагается реализовать под собственные нужды.