Крупногабаритное литье для автопрома: собрали и запустили в работу двухплитный большой ТПА 1000 в цехе ограниченной высоты
Заказчик — не новичок в полимерной отрасли
Предприятие в Ульяновске, оборудованное термопластавтоматами, разрабатывает и изготавливает пластиковые комплектующие и детали узлов и агрегатов для автомобильной отрасли с 2005 года. Основная номенклатура: автомобильные коврики, колодки, крышки корпуса термостата, шестерня распределительного вала, крышки клапанов, крышки маслоналивной горловины и прочее.
В структуре свой литьевой участок из 7 горизонтальных ТПА от 50 до 600 т и несколько десятков единиц вспомогательного оборудования, а также инструментальный цех по изготовлению пресс-форм, в том числе с габаритами до 1100-1200 мм.
Наше первое знакомство состоялось в 2021 году, когда производитель расширял и модернизировал парк машин, закупив в «Интерпласт» два ТПА усилием 50 и 200 тонн. Они работают исправно и не вызывают нареканий по сей день.
В условиях положительной динамики внутреннего рынка в связи с активным восстановлением российского автопрома — автомобильное литье под давлением становится одним из привлекательных сегментов в полимерной индустрии.
Проблема масштабируемости
Завод постоянно осваивает новые изделия. И в этот раз искал технологическое решение для выпуска крупногабаритных деталей, в частности пластиковых крышек двигателя. Пытались делать на существующем оборудовании, но не получилось. Исходя из производственных потребностей, понадобился крупнотоннажный термопластавтомат.
Принципы выбора литьевой машины
Предприятие планировало вложить 20-30 млн руб. в расширение литьевого участка и за эти деньги купить ТПА с комплектом вспомогательного оборудования.
Производитель получил предложения от нескольких поставщиков с большим диапазоном технических характеристик оборудования и стоимости заказа, с разницей в 1,5 раза между самым бюджетным и дорогим предложением.
Выбор литьевой машины зависел одновременно от следующих параметров:
- усилие смыкания — 1000 т;
- эффективная масса впрыска — не менее 4 000 г;
- наличие шнековой пары для работы со стеклонаполненным сырьем;
- возможность работы в цехе ограниченной высоты.
Для реализации проекта выбрали предложение «Интерпласт» с учетом надежности поставщика и предыдущего опыта сотрудничества, стоимости изготовления, доставки и монтажа оборудования. Существенное значение имели своевременно выявленные проблемы клиента и сформированные задачи по технологической модификации конструкции ТПА.
Стоит помнить, что при выборе сложного промышленного оборудования экономия денег довольно опасна. Купив дешевую машину, в процессе эксплуатации можно вложить в нее в разы больше, чем она изначально стоила.
Комплексная организация участка крупногабаритного литья
Исходные данные для проработки технического предложения
- Чертежи на детали
- Общий вид пресс-формы и скрины с моделей пресс-формы
- Сырье — стеклонаполненный полиамид Па6.6-Св30
Требовались только литьевая машина и периферийное оборудование, поскольку пресс-формы заказчик делает на своем заводе. При этом все должно работать в комплексе и поставлено единовременно с проведением необходимых пусконаладочных работ поставщиком.
«Интерпласт» полностью оборудовал цех следующим оснащением:
- термопластавтомат DP1000-S6 i9500 с биметаллической шнековой парой для увеличения срока службы при работе с полиамидом, усиленным стекловолокном;
- увеличенный узел смыкания;
- специализированный контроллер для каскадного литья на 8 гидроклапанов и горячеканальной системы на 8 каналов;
- робот-манипулятор с захватом для снятия деталей;
- конвейер длиной 3 м для перемещения детали от робота к рабочему месту;
- термостат;
- чиллер;
- сушильная установка «3 в 1» с системой осушения и влагоотделения, автоматической загрузкой;
- хранилище для материала на 300 кг.
ТПА серии DP1000 — это большая высокоскоростная двухплитная литьевая машина с горизонтальным впрыском. Отличается увеличенным шнеком диаметром 110 мм, усилием смыкания 1000 тонн, силой зажима 10 000 кН, максимальной массой впрыска 4 972 г и объемом впрыска 5 464 см3.
Ключевые общие характеристики серии DP
- Компактные размеры, длина примерно на 10-20 % короче, чем трехплитной машины.
- Повышенная производительность и точное позиционирование за счет быстрого открытия/закрытия и большого хода пресс-формы.
- Удобство смены оснастки с возможностью низкой установки.
Нет необходимости покупать трехплитную машину большего размера. Двухплитный ТПА снижает инвестиционные затраты на приобретение оборудования и экономит пространство. Быстрое открытие пресс-формы сокращает производственный цикл и повышает эффективность производства.
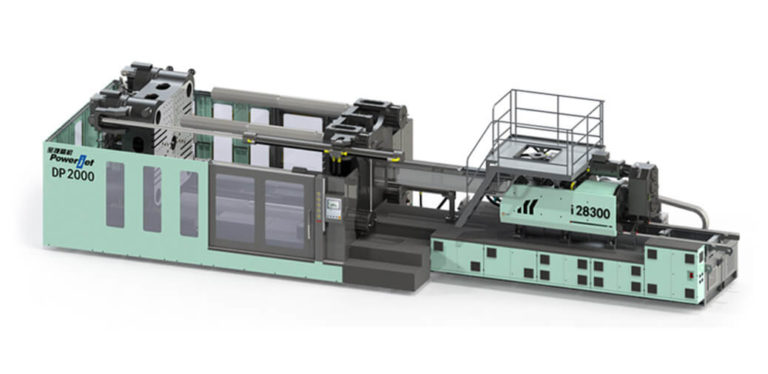
Термопластавтоматы для крупногабаритного литья
Для автоматизации литья под давлением на разных уровнях предложили сушилку, термостат и чиллер. Следует отметить, что только внедрение комплексной автоматизации может обеспечить повышение производительности оборудования: ускорить процесс подготовки полимерного сырья и производства изделий из пластика.
Оборудование подбирали, отталкиваясь от цикла и веса изделия. Непростым оказался подбор сушилки. Клиент настаивал на более компактном варианте, но в итоге принял решение, основанное на четких расчетах.
Пример расчета, выполненный для заказчика
|
Объем компактной сушилки L: 3600с÷60с*2кг*5ч/0.7=857L При меньшем времени цикла сушилка была бы больше |
Подчеркнем, что для ускорения сушки недостаточно просто подавать горячий воздух. Необходимо принудительно отводить влагу. К этому приспособлено сушильное оборудование серии «3 в 1» с системами осушения и влагоотведения.
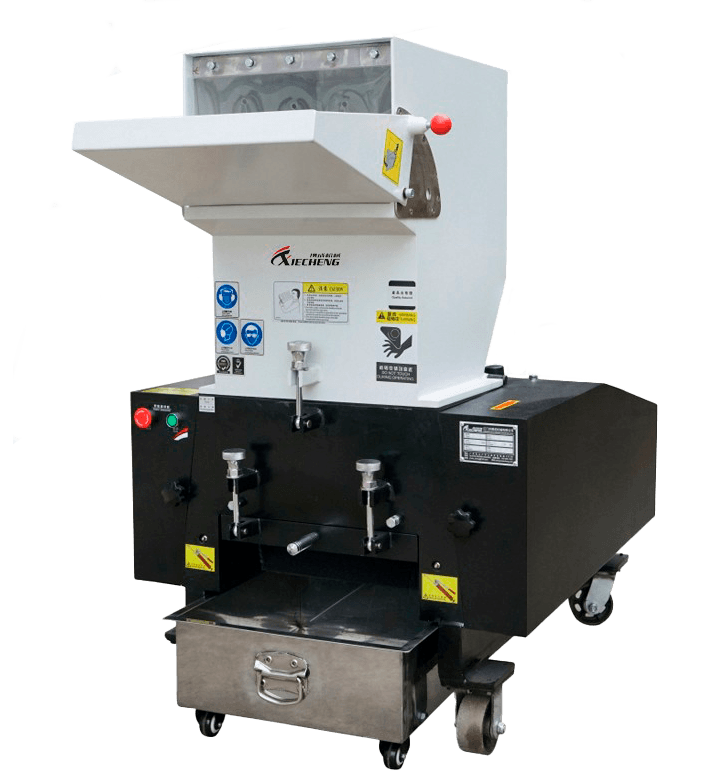
Вспомогательное оборудование для производства полимеров
Оборудование, поставки которого невозможно организовать в полностью собранном виде
Крупнотоннажное полимерное оборудование ставит перед поставщиками задачу сборки на месте. Мы имели дело с большой машиной массой 43 тонны, которую невозможно перемещать в собранном виде и перевозить одним контейнером. Поэтому ТПА спроектирован и изготовлен так, что его можно перевозить в разобранном виде отдельными узлами и деталями разной массы.
С завода отправили три контейнера в пункт назначения. Новизной перевозки стало наличие негабаритного груза, под который потребовался специальный трал. Работали в рамках одной внешнеэкономической сделки, организацию и сопровождение которой полностью взяли на себя.
В итоге поставки комплекса, включающего ТПА DP1000 с комплектом периферийного оборудования поступили:
- рама узла смыкания — 5 т;
- неподвижная плита узла смыкания — 7 т;
- узел впрыска — 7,5 т;
- подвижная плита узла смыкания — 11 т;
- вспомогательное оборудование — 2 010 кг.
После того, как клиент получил оборудование, его предстояло собрать с нуля и протестировать, что требует значительных трудозатрат по сборке и серьезной материально-технической подготовки. Работы клиент доверил инженерам «Интерпласт», чтобы избежать дорогостоящих ошибок. Как только наладчики убедились, что все подвижные части на оборудовании работают правильно, они приступили к пуско-наладочным работам.
Как менять пресс-форму
Литьевая оснастка обычно заводится сверху между колоннами с помощью кран-балки, погрузчика или других грузоподъемных механизмов. Однако в нашем случае было помещение с низким потолком: кран-балка имеется, но поскольку она закреплена невысоко, а термопластавтомат высокий, между ними места не хватает для установки пресс-формы таким способом.
Предложили оптимальное решение — заводить сбоку. Для этого сконструировали ТПА таким образом, чтобы подвижная плита плавно отъезжала за пределы колонн за счет увеличенной длины рамы узла смыкания, благодаря чему освобождается пространство, куда можно завести пресс-форму за колоннами и присоединить ее к подвижной плите.
Технический плюс в том, что в процессе не задействованы колонны ТПА: если бы они ездили туда-сюда при каждой смене оснастки, то движущая их система быстро бы изнашивалась. В связи с этим постепенно бы нарушалась параллельность расположения колонн, а перекос при таких массах и нагрузках, как на больших термопластавтоматах, крайне критичен для всего процесса литья. В худшем случае все закончится тем, что колонна лопнет, ее замена будет стоит огромных денег, а ждать деталь придется несколько месяцев, поскольку на складах никто их не держит. Нам удалось это предусмотреть и защитить производство от убытков и простоя.
Заключение
Расширение ассортимента продукции на предприятии — это тот триггер, который обеспечивает рост производства и увеличивает прибыль. Решение данных задач часто реализуется посредством внедрения нового оборудования, в том числе больших литьевых машин.
В практике «Интерпласт» ТПА DP1000 оказался самой крупнотоннажной моделью для литья под давлением. Благодаря большому техническому опыту и детальному планированию всех работ компании удается предусмотреть риски, которые могут возникнуть на производстве клиента, и минимизировать их последствия, запустить проверенное на работоспособность и производительность оборудование. На первый взгляд ничего нового, но суть, как всегда, в экспертности.