Модифицировали изделие, убрав закладную часть, поставили пресс-формы для производства мебельной ножки и сняли ТПА с пятилетней консервации
Все чаще производители самых разных отраслей (необязательно полимерной) задумываются о своем производстве деталей, комплектующих или упаковки для своей продукции, чтобы не зависеть от растущих цен, перебоев с доставкой и нестабильным качеством поставщиков. Контролировать и влиять на ситуацию без посредников куда проще, учитывая обстоятельства последних двух лет.
Примеры производителей, которые уже поняли выгоды от предприятий «полного цикла»:
- Компании, оказывающие услуги по проведению электрокоммуникаций и изготовлению электросчетчиков теперь изготавливают пластиковые корпуса для счетчиков самостоятельно.
- Производители труб, которые делают фитинги для своей продукции.
- Производители торгового и холодильного оборудования, наладившие производство мягких профилей ПВХ для ценникодержателей и заглушек.
- Строительные компании, которые начинают производить различные детали/панели/профиль для строительства своими силами.
Суть проекта
В этом кейсе расскажем про компанию, занимающуюся выпуском деревянной мебели для ванных комнат, которая впоследствии стала выпускать мебельные ножки для своих нужд и планирует продолжать развивать это направление.
История началась с того, что клиент был готов инвестировать в восстановление другого предприятия, но по прошествию времени все изменилось. Заказчик задумался о том, чтобы поставить на своем производстве термопластавтомат, закупить пресс-формы и наладить производство изделий для своей же деревянной мебели.
При этом совершенно не имея опыта в полимерном производстве, клиент не испугался и начал поиски оборудования и оснастки. Изготавливая мебель на деревообрабатывающих станках, ранее он закупал ножки для шкафчиков у российских поставщиков. Эти ножки были с металлической частью (болтом), а остальная часть изделия была из пластика.
Модификация изделия и решение
Изделие «мебельная опора» состоит из двух частей: верхней и нижней, общий вес изделия 35 г. То есть необходимо было разработать две пресс-формы. Здесь мы всегда запрашиваем образец изделия, чертеж или 3D модель.
В процессе согласования изделия, заказчик уточнил, что хотел бы доработать изделие и убрать металлическую часть из нижней части. Чтобы не создавать дополнительных сложностей, сократить время сборки изделия и снизить его себестоимость. Вместо металлического болта мы сделали пресс-форму под пластиковый, и это решение полностью устроило заказчика. Функционально в изделии ничего не изменилось.
В результате получилось: 2 холодноканальных пресс-формы с теоретическим циклом 30 и 40 секунд, на 8 и 12 гнезд соответственно.
Согласование образцов
Согласование образцов прошло быстро. Завод изготовил и прислал образцы, отлитые на первичном полимерном сырье. Клиент попросил опробовать эти же пресс-формы на вторичном сырье. Мы выполнили требование, выслали видео получившихся изделий и не дожидаясь посылки с изделиями, клиент все согласовал и внес оплату.
После этого завод подготовил пресс-формы к отгрузке и теперь оставалось только ждать доставки оснастки.
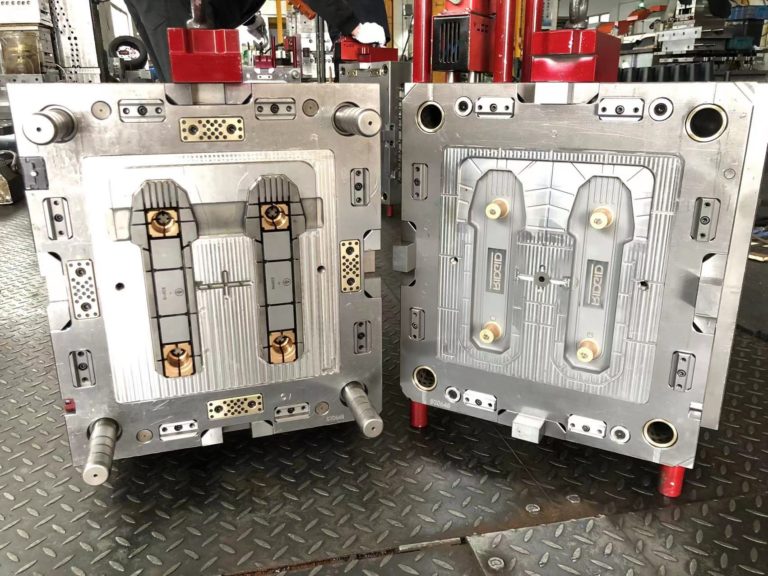
Пресс-формы для литья пластмасс
Ввод в эксплуатацию
Для своих нужд клиент подобрал подходящий б/у ТПА, чтобы при невысоких потерях оценить выгоды работы. Когда оснастка была доставлена, наши инженеры-наладчики выехали на предприятие клиента, чтобы ввести пресс-формы в эксплуатацию.
Им удалось запустить термопластавтомат, который до этого момента стоял на консервации около 5 лет, настроить производственный цикл и требуемое качество изделий. Владелец предприятия и персонал остались очень довольны работой сервисных инженеров и даже оставили небольшой видеоотзыв.
Планы
Клиент планирует закупить оборудование для вакуумной покраски изделий под металл, а также наладить производство пластиковой «мебельной ручки». Для этого ему понадобится расширить парк оборудования и заказать оснастку, наш технический отдел уже работает над этим проектом.
Подытожим
В результате в этом проекте нам удалось убить нескольких зайцев одним выстрелом:
- разработали пресс-формы под требуемое изделие с оптимальным временем цикла
- сократили для клиента время на изготовление и на сборку изделия, внеся доработки
- снизили тем самым себестоимость изделия
- помогли не только ввести пресс-формы в эксплуатацию, но и настроить ТПА для работы, чем значительно приблизили дату запуска производства.
Познакомиться с другими реализованными проектами можно на нашем сайте или в социальных сетях. В списке наших кейсов не только работа с изготовлением и запуском новых пресс-форм в производство, но поставки ТПА и периферии и контрактное литье. А в нашей базе знаний вы найдете массу полезных лайфхаков по организации производства, наладке литьевого и повышению эффективности работы оборудования и персонала.